Imagine a massive air purifier that cleans industrial pollutants from gas streams – that’s what an Industrial Scrubber does, but with incredible precision.
Working in chemical plants, I’ve seen these systems transform heavily polluted gas into clean emissions that meet strict environmental standards.
The core principle involves polluted gas meeting a special cleaning liquid (solvent), where pollutants naturally move from the gas into the liquid, much like sugar dissolves in coffee. The cooler the temperature, the better this process works.
The solvent choice is crucial – water works great for inorganic pollutants, while special oils catch organic compounds that water can’t trap.
By thoroughly understanding these aspects of Gas Absorption and industrial scrubbers, engineers and operators can make informed decisions about implementation and maintenance.
This knowledge ensures optimal air quality control in industrial processes while managing costs and meeting environmental requirements.
Regular monitoring, combined with proactive maintenance and optimization, keeps these critical systems operating at peak efficiency for years to come.
Types of Industrial Scrubbers
The first and most efficient type is the packed tower scrubber. Picture a tall column filled with specialized materials that create extensive surface area for gas-liquid contact.
These towers excel at removing up to 99.9% of pollutants while handling high-speed gas flows and using minimal water. Though highly effective, they require careful maintenance to prevent clogging and ensure consistent performance.
Tray column scrubbers function like a multi-story building, where each floor (tray) creates a meeting point for gas and liquid.
Built from durable stainless steel, these scrubbers effectively resist corrosion and handle temperature changes well, thoroughly cleaning gas at each level. While they’re incredibly robust, they do demand more operational power compared to other designs.
Venturi scrubbers are the champions at catching tiny particles and sulfur dioxide. Their narrow throat design creates powerful gas-liquid mixing, enabling them to catch particles as small as 0.5 micrometers with impressive removal efficiency.
The main trade-off comes in higher energy consumption due to significant pressure drops, making them best suited for specific applications where fine particle removal is crucial.
Spray column scrubbers represent the simplest design that still delivers strong results. Using strategically placed spray nozzles, they offer easy maintenance and low energy consumption while maintaining effective operation.
This makes them ideal for operations that need reliable performance without excessive complexity. Their straightforward design means fewer things can go wrong, though they might not achieve the same peak efficiency as more complex systems.
Gas Absorption and Industrial Scrubbers
Flow Configurations and Performance
The way gas and liquid move through the scrubber dramatically affects its performance. Countercurrent flow, where gas and liquid move in opposite directions, proves most effective for most applications.
Cross-current flow, with gas moving horizontally while liquid flows down, offers a middle-ground solution. Co-current flow, where both gas and liquid move in the same direction, works well in specific situations but generally provides lower efficiency.
Several key elements determine scrubber effectiveness: contact time between gas and liquid, surface area for interaction, solvent temperature and chemistry, gas flow rate, and pollutant concentration all play crucial roles. Regular maintenance ensures these factors remain optimized for peak performance.
Selecting the Right Scrubber
Choosing an ideal scrubber requires careful consideration of multiple factors. The type and concentration of pollutants form the primary consideration, followed by required removal efficiency and gas flow volume.
Available space, energy costs, maintenance capabilities, and environmental regulations also significantly influence the decision. A thorough analysis of these factors helps ensure the selected system meets both current needs and future requirements.
Maintenance and Long-Term Success
Experience shows that well-maintained scrubbers can operate effectively for decades. Essential maintenance involves regular inspection of all components, including cleaning of nozzles and packing materials, monitoring pressure drops, chemical analysis of cleaning solutions, and prompt repair of any leaks or damage.
This proactive approach prevents minor issues from developing into major problems that could compromise system performance.
Real-World Performance and Optimization
Most industrial scrubbers achieve between 90% and 99.9% pollutant removal when properly designed and maintained. This impressive efficiency stems from optimal gas-liquid contact, correct solvent selection, proper temperature control, regular maintenance, and skilled operation.
Actual performance depends heavily on initial pollutant concentration, gas flow characteristics, operating conditions, system design quality, and maintenance practices.
Temperature control plays a particularly crucial role in system efficiency. Lower temperatures generally improve absorption rates, but operating too cold can create other issues like condensation or increased energy costs.
Finding the right balance requires understanding both the chemistry involved and the practical limitations of your system.
The chemical composition of the cleaning solution also significantly impacts performance. While water serves as an excellent solvent for many applications, some situations require specialized solutions.
These might include caustic solutions for acid gas removal or specific organic solvents for hydrocarbon capture. The choice of solution must balance effectiveness against cost and environmental impact.
Final Thoughts
Understanding pressure drop across the system helps optimize performance while managing energy costs.
Too little pressure drop might indicate insufficient contact between gas and liquid, while excessive pressure drop wastes energy and might signal problems like clogging or flooding.
Regular monitoring helps maintain optimal operation while identifying potential issues before they become serious problems.
Author Profile
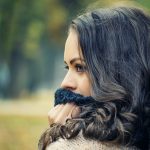
- Blogger by Passion | Contributor to many Business Blogs in the United Kingdom | Fascinated to Write Blogs in Business & Startup Niches |
Latest entries
BusinessSeptember 2, 2025Professional Office Cleaning Services in Canary Wharf
Home & LivingSeptember 1, 2025Why Herringbone Floors Are Everywhere Again?
FinanceSeptember 1, 2025Taking Back Control: Essential Insights Into Car Finance Claims and PCP Claims
Social MediaAugust 29, 2025Best Sites to Buy Instagram Likes: 9 Providers Ranked & Tested