Workplace safety regulations are critical for ensuring a safe environment for employees. These regulations, set by governmental bodies, aim to minimise risks associated with various workplace hazards. Adhering to these regulations not only protects employees from harm but also helps businesses avoid legal penalties and maintain a good reputation. Key regulations often cover the handling and storage of hazardous materials, use of personal protective equipment (PPE), emergency procedures, and regular safety training.
Compliance with safety regulations involves understanding and implementing specific guidelines relevant to your industry. Regular risk assessments should be conducted to identify potential hazards and implement appropriate control measures.
This might include installing proper storage solutions for hazardous substances, ensuring all employees are trained in safety protocols, and maintaining equipment to prevent malfunctions. By staying informed about the latest regulations and incorporating them into daily operations, businesses can create a safer workplace and enhance overall productivity.
Top Strategies for Maintaining a Safe Work Environment
Common Types of Hazardous Substances in the Workplace
Identifying hazardous substances present in your workplace is a crucial step towards ensuring safety. These substances can vary widely depending on the industry, but common examples include chemicals, flammable materials, and biological agents. Chemicals such as solvents, acids, and cleaning agents pose significant health risks if not handled correctly. Flammable materials, including certain liquids and gases, can easily ignite and cause fires or explosions if stored improperly
.
Biological agents like bacteria, viruses, and other pathogens are particularly relevant in healthcare and laboratory settings. Workplaces might encounter hazardous dust and fumes from manufacturing processes. Understanding the risks of hazardous substances in your environment allows you to implement targeted safety measures.
Proper labelling, usage instructions, and personal protective equipment are vital components of handling these materials safely. Regular training and updates on handling protocols ensure that all employees are aware of the risks and procedures.
Best Practices for Storing Hazardous Materials
Storing hazardous materials correctly is essential for maintaining a safe workplace. One of the primary practices is segregating incompatible substances to prevent dangerous reactions. This can be achieved by using dedicated storage cabinets designed for specific types of hazardous materials. For instance, flammable liquids should be stored in flame-resistant cabinets, while acids and bases need separate, non-reactive storage solutions.
Ventilation is another critical factor. Properly ventilated storage areas help disperse harmful vapours and reduce the risk of inhalation. Clearly labelling all storage containers with the contents and associated hazards ensures that everyone is aware of the potential risks.
Regularly inspecting storage areas for leaks, corrosion, or other signs of deterioration can prevent accidents before they occur. Ensuring that all storage cabinets and containers are securely closed when not in use further enhances safety. By following these best practices, businesses can effectively minimise the risks associated with hazardous materials.
Enhancing Workplace Safety with COSHH Cabinets
Implementing COSHH (Control of Substances Hazardous to Health) cabinets is an effective way to enhance workplace safety. These specialised storage cabinets are designed to contain hazardous substances securely, preventing accidental exposure or spills. Using COSHH cabinets ensures that dangerous chemicals and materials are stored in compliance with health and safety regulations, thereby reducing the risk of workplace accidents.
In addition to storage, COSHH cabinets offer features such as built-in ventilation and spill containment, which further protect employees from hazardous fumes and leaks. When selecting a storage solution, it is essential to choose a cabinet that meets the specific requirements of the substances you are storing. This might include factors like resistance to corrosion, appropriate labelling, and secure locking mechanisms. Regular maintenance and inspections of these cabinets help ensure they remain effective over time.
Training employees on the correct use of COSHH cabinets is equally important. Workers should be familiar with the safety protocols for accessing and handling hazardous substances. By incorporating these cabinets into your safety strategy, you can create a safer and more compliant workplace, ultimately protecting your employees and your business from potential hazards.
The Benefits of Investing in Quality Storage Cabinets
Investing in quality storage cabinets offers numerous advantages for workplace safety and efficiency. High-quality cabinets are designed to withstand the demands of industrial environments, ensuring that hazardous substances are securely contained. This reduces the risk of spills, leaks, and accidental exposure, which can lead to serious health and safety incidents. Durable materials and robust construction mean these cabinets can endure harsh conditions, providing long-term protection for your hazardous substances.
In addition to safety benefits, quality storage cabinets can enhance the organisation within your workplace. Properly labelled and designated storage areas make it easier for employees to locate and access the materials they need, reducing downtime and increasing productivity. Efficient use of space also helps to maintain a clean and orderly work environment, which can further contribute to overall safety and operational efficiency. By investing in high-quality storage solutions, businesses can protect their employees and assets while improving workplace functionality.
Training Employees on Safe Storage Practices
Proper training ensures that everyone understands the risks associated with hazardous materials and knows how to handle them safely. This includes educating employees on the correct use of personal protective equipment (PPE), how to read and interpret safety data sheets (SDS), and the importance of following established safety protocols.
Effective training programmes should also cover the proper storage procedures for various hazardous substances. Employees need to be aware of the specific storage requirements for different types of materials, such as flammable liquids, corrosive chemicals, and reactive substances.
This training should include hands-on demonstrations and regular refresher courses to keep safety practices top of mind. Additionally, creating a culture of safety where employees feel comfortable reporting potential hazards or unsafe conditions can significantly reduce the risk of accidents. By investing in comprehensive training, businesses can ensure a safer environment for everyone.
How Proper Storage Can Prevent Workplace Accidents?
Proper storage of hazardous substances is crucial in preventing workplace accidents. Incorrect storage can lead to dangerous chemical reactions, spills, and exposure to toxic substances, all of which pose significant risks to employee health and safety. Implementing appropriate storage solutions, such as hazardous substance cabinets, mitigates these risks and creates a safer work environment.
Effective storage solutions should include secure locking mechanisms, clear labelling, and adequate ventilation to manage fumes and vapours. Regular maintenance and COSHH inspections ensure that storage cabinets remain in good condition and continue to provide protection. Proper training for employees on storing and handling hazardous materials safely is crucial.
This includes understanding the importance of keeping storage areas clean and organised and knowing how to respond in the event of a spill or other incident. These measures significantly reduce the likelihood of accidents and enhance overall workplace safety.
Ensuring the proper storage of hazardous materials is vital for maintaining a safe and efficient workplace. By understanding the specific hazards present and implementing best practices for their storage, you can significantly reduce the risk of accidents and health issues. Quality storage cabinets, tailored to the needs of different substances, play a crucial role in this process. They provide secure and organised solutions that prevent spills and exposures.
Regular maintenance of these storage solutions, along with comprehensive employee training, further enhances safety. Employees must be well-versed in handling and storing hazardous materials, using appropriate personal protective equipment, and responding effectively to potential incidents. Creating a culture of safety, where reporting hazards and adhering to protocols is encouraged, contributes to a safer work environment. Prioritising these measures protects both employees and your business, fostering a productive and secure workplace.
Author Profile
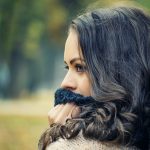
- Blogger by Passion | Contributor to many Business Blogs in the United Kingdom | Fascinated to Write Blogs in Business & Startup Niches |
Latest entries
Social MediaJuly 1, 2025TikTok AI Dance Revolution: Top Trends, Earnings & How to Go Viral
CareerJune 18, 2025How to Apply for the PEBC Exam as an International Pharmacy Graduate in 2025?
FinanceJune 14, 2025BlackRock: The World’s Most Powerful Asset Manager Explained
Home & LivingMay 6, 2025Top 5 Used Fuel Efficient Cars for UK Drivers